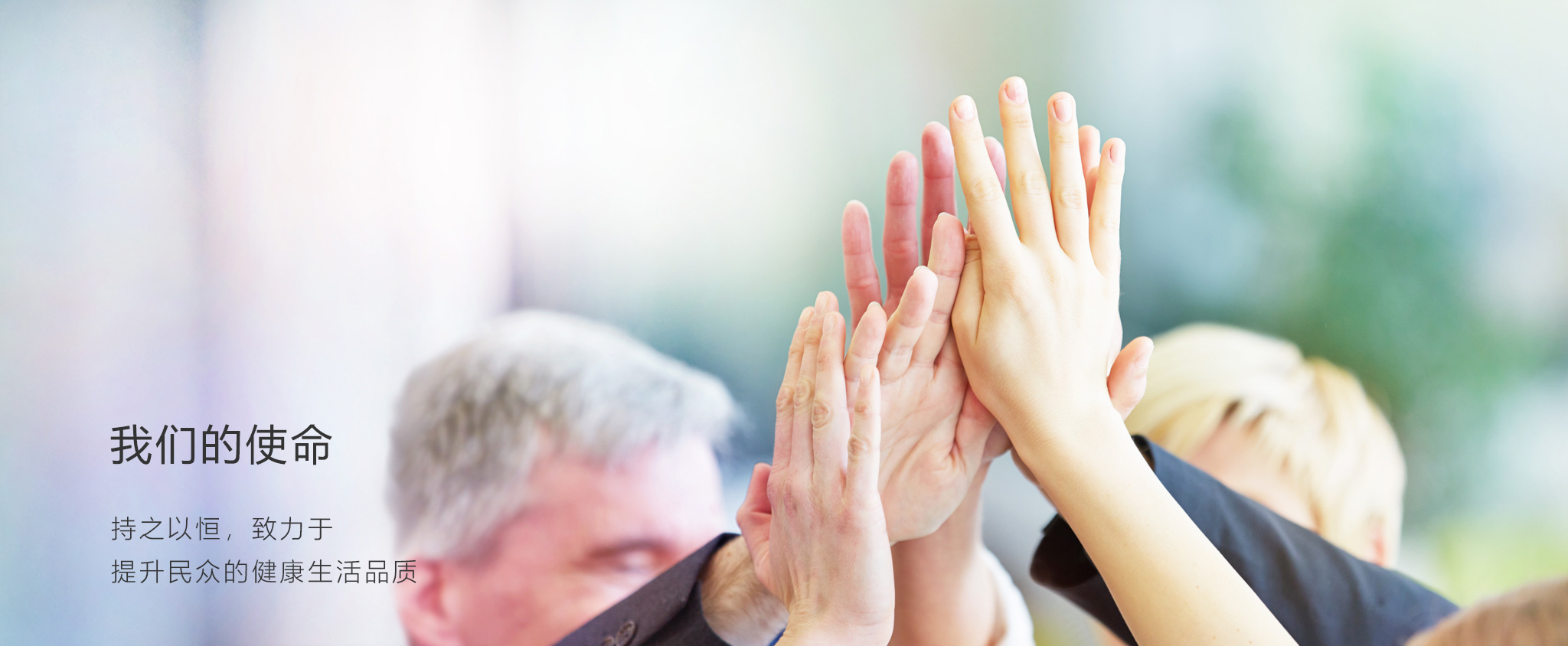
西格玛计算公式如下:∑(2i+1)表示和式:(2*2+1)+(2*3+1)+(2*4+1)+...+(2*10+1)=222。i=2,式子中的2i+1是数列的通项公式Ai,i是项的序数,i=2表示从数列{2i+1}的第二项开始计算,顶上的10是运算到的10项截止。
顶上的10是运算到的10项截止。大写Σ用于数学上的总和符号,比如:∑Pi,其中i=1,2,...,T,即为求P1 + P2 + ... + PT的和。小写σ用于统计学上的标准差。西里尔字母的С及拉丁字母的S都是由Sigma演变而成。也指求和,这种写法表示的就是∑j=1+2+3+…+n。
看下面的图表就知道了。是计算出来的。DPU=不合格数/单位数(也就是经过某个控制点的被测物总数)DPMO=DPU*1000000/每个单位出错机会数。简单的说,6西格玛的水平相当于每100万件产品中只出错4件。而且是全系统的水平,不是单个控制点的水平,难度很高。
1、六西格玛是一项以数据为基础,追求几乎完美的质量管理方法。西格玛是一个希腊字母σ的中文译音,统计学用来表示标准偏差,即数据的分散程度。对连续可计量的质量特性: 用“σ”度量质量特性总体上对目标值的偏离程度。几个西格玛是一种表示品质的统计尺度。任何一个工作程序或工艺过程都可用几个西格玛表示。
2、六西格玛的含义:西格玛在概率统计学里的含义为“标准偏差”,用σ表示。6σ意为“六倍标准差”,在质量管理上代表着品质合格率达99997%以上,或者可以表示为每百万个产品或操作中失误少于4。但是六西格玛的含义并不简单的指上述统计上的要求,而是一整套系统的理论和实施方法。
3、引言六适马(6适马)是一种管理战略,由当时在摩托罗拉工作的工程师比尔·史密斯于1986年提出。这种策略主要强调设定极高的目标,收集数据,分析结果,通过这些可以减少产品和服务的缺陷。
4、六西格玛也称Six Sigma和6 Sigma,是一种管理策略,主要倾向于品质管理,由摩托罗拉1986年提出。这种策略强调制定极高的目标、收集数据以及分析结果,通过这些来减少产品和服务的缺陷。六西格玛背后的原理就是如果你检测到你的项目中有多少缺陷,你就可以找出如何系统地减少缺陷,使你的项目尽量完美的方法。
为了提高质量,工厂的管理者们发明了“六个西格玛”管理方法。“西格玛”是统计学里的一个单位,表示与平均值的标准偏差。它可以用来衡量一个流程的完美程度,显示每100万次操作中发生多少次失误。“西格玛”的数值越高,失误率就越低。
西格玛“s”是希腊字母,在统计学上用来表示数据的分散程度。对连续可计量的质量特性,可用“s”度量质量特性总体上对目标值偏离程度(见图1所示),6西格玛质量表示质量特性的分散程度只占规格限的一半。对顾客要求高度符合。在以缺陷率计量质量特性时,用“s”度量缺陷率。
分别指的是人(Man)、机器(Machine)、物料(Material)、方法(Method)、环境(Environments)、测量(Measure),简称人、机、料、法、环、测。人员(Man)人员是生产过程中的核心要素,涵盖从基层操作员工到管理层的所有人员。人员的专业技能、工作态度以及质量意识都直接影响产品的质量。
σ质量管理方法6σ管理法是一种统计评估法,核心是追求零缺陷生产,防范产品责任风险,降低成本,提高生产率和市场占有率,提高顾客满意度和忠诚度。6σ管理既着眼于产品、服务质量,又关注过程的改进。
在质量管理中,六要素分别包括以下内容: 人:操作者对质量的认识、技术熟练程度、身体状况等。 机:机器设备、测量仪器的精度和维护保养状况等。 料:材料的成分、物理性能和化学性能等。 法:包括生产工艺、设备选择、操作规程等。 环:主要指测量时采取的方法是否标准、正确。
六西格玛(Six Sigma)是一种改善企业质量流程管理的技术,以“零缺陷”的完美商业追求,带动质量大幅提高、成本大幅度降低,最终实现财务成效的提升与企业竞争力的突破。项目实施 对需要改进的流程进行区分,找到最有潜力的改进机会,优先对需要改进的流程实施改进。
六西格玛是一种管理业务和部门的系统方法。它把顾客放在第一位,它是利用事实和数据来驱动更好地解决问题的方法。六西格玛项目主要有三个领域:a).提高顾客满意 b).缩短工作周期 c).减少缺陷。这些领域的改善通常意味着业务费用的显著节省,留住客户机会的增加,以及建立高层次产品和服务的声誉。
中间有漂移。用百万分之缺陷率(ppm)来表示过程能力,一般可以通过测量缺陷的比率,估算过程的西格玛水平,并以此考察过程满足顾客要求的能力。 当分布中心无漂移时,即样本均值与分布中心重合时,3西格玛水平对应的不合格率为0.27%,即2700ppm;6西格玛水平对应的不合格率为十亿分之二,即0.0024ppm。
六西格玛(Six Sigma,6 Sigma)是一种管理策略,它是由当时在摩托罗拉任职的工程师比尔史密斯(Bill Smith)于1986年提出的。这种策略主要强调制定极高的目标、收集数据以及分析结果,通过这些来减少产品和服务的缺陷。